Deburring on the Cutting Edge
“It wasn’t and isn’t a glamorous field, but that perception is changing,” says Anton Bax. “Because it’s just too expensive to manually deburr all your sheet metal with an angle grinder.” Moreover, the demands in the industry and among end customers continue to rise. They are not only concerned with removing all burrs, but sheet metal parts need to be finished in a hand-friendly manner. “For thin sheet metal parts, such as stainless steel, a small rounding is often sufficient, while for thicker steel parts, a larger edge rounding is increasingly required because it improves paint coverage. Paint adheres less well to sharp corners.”
“The logical next step is the automation of the loading and unloading process with robots.”
Bax is a born entrepreneur. Over thirty years ago, he joined his father’s own sheet metal production company, Bax Metaal. By now, the industrial area on the west side of Bergeijk is filled with offshoots: Laserparts, RVS Finish, and the youngest member: machine builder Q-Fin, an abbreviation for Quality Finishing Machines. Before summer, a second facility needs to be built because business is thriving, and Q-Fin wants to continue growing.
New Course
With the establishment of Q-Fin in 2013, Bax took a step in a different direction. He had never before been actively involved in the development and construction of his own machines. He is glad that he split his organization into multiple companies, allowing him to focus on the development of Q-Fin. “For me, Q-Fin is something new; it’s our own product, establishing a global market presence, building customer relationships, and convincing them of the concept of our machines. I find that a wonderful challenge.”
Bax is ambitious but also very down-to-earth: “We shouldn’t grow too fast because our factory is already full. We’ve built a good reputation in the Netherlands in recent years. Our market focus is now on Germany, where there is still a lot for us to gain. Particularly due to the emphasis on handling around deburring machines, projects are becoming larger. Hence, the planned new construction that provides us with space to expand further.”
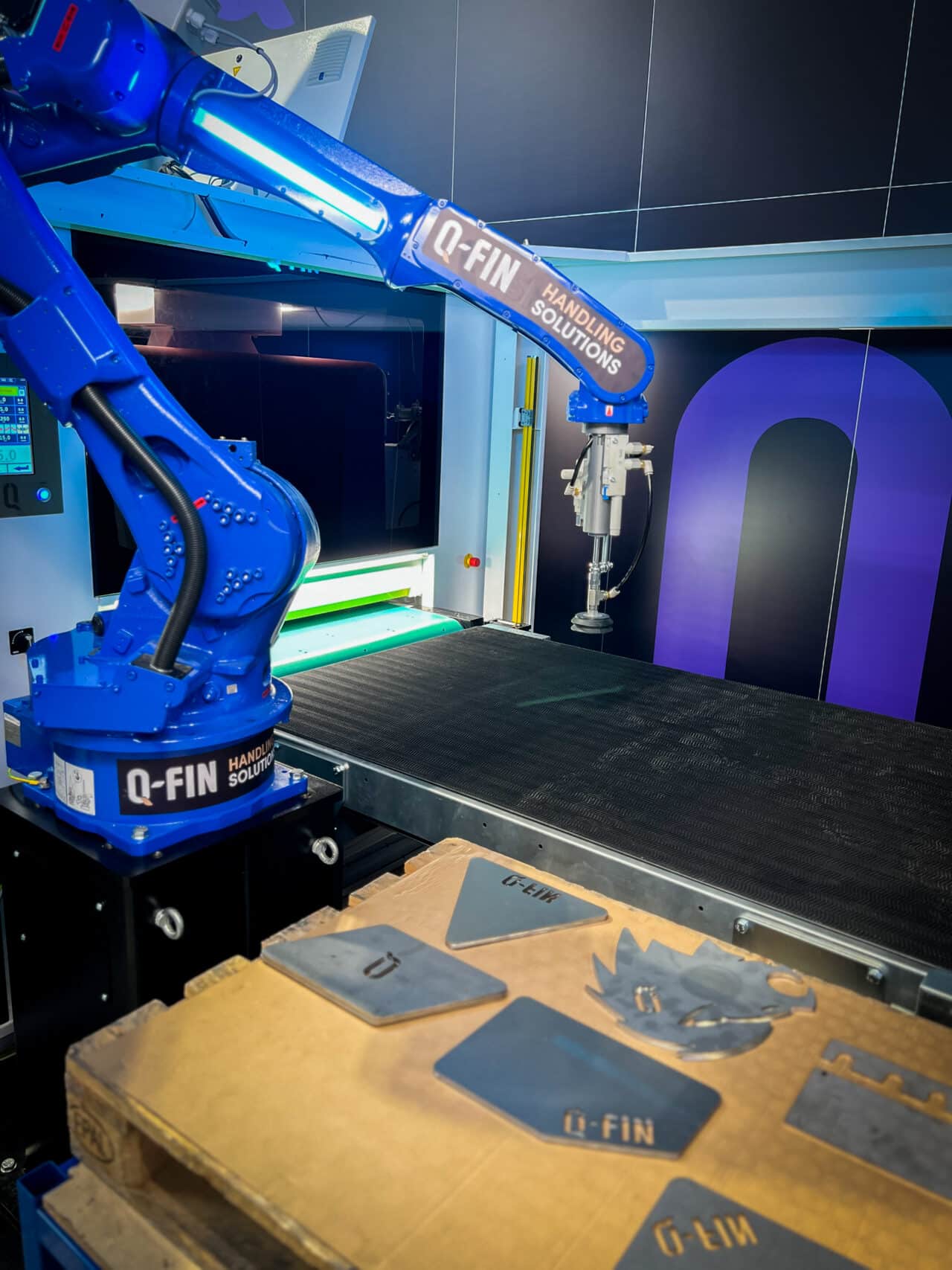